Get in Touch
Dr Victor Zhitomirsky | Managing Director
victor.zh@camencoders.comPhone: +44 (1223) 560996 | Mobile: +44 (7722) 949627
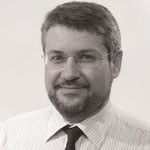
18-bit resolution for 58mm, 19-bit resolution for 25mm through-hole encoders
Copyright © 2020 CamEncoders- All Rights Reserved